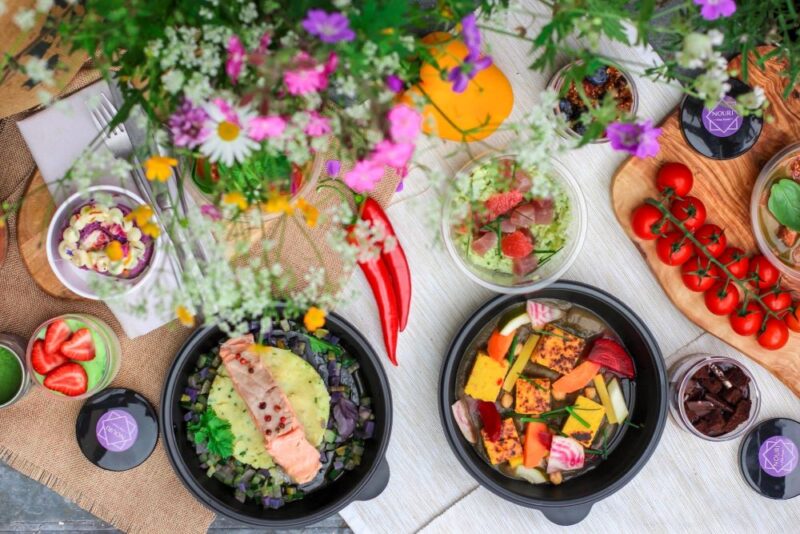
「食品工場」の仕事と言うと、「ベルトコンベア」で流れてくる弁当に盛り付けする「ライン作業」を想像される方も多いと思います。
「フルオートメーション」で工場内に人がほとんどいない「食品工場」を想像される方は少ないのではないでしょうか?
国内にある「食品工場」の事業所数は、なんと「2万3千事業所」あまりにもなります!!
これが多いのか少ないのか?
大手コンビニの店舗は合わせて「約5万店舗」ですので・・・(数の参考です)
とにかく多いです
そしてその99%が中小零細企業なのだそうです。
20年も食品会社に勤務しているにも関わらず、はじめて知りました。
中小零細の「食品工場」が日本の食文化を支えている訳です。
さらに「食品工場」で勤務しているのは「多くのパートさん」です。
毎日の作業「本当にお疲れ様です!!」
この場を借りて感謝を伝えます。
求人広告でも必ずと言っていいほど掲載されているのが「食品工場」です。
「経験不問で未経験者歓迎!!」って、ブラック企業の代表的な案内ですので不安になりませんか?
そんな「食品工場」では「どのような作業を行っているのか?」
そして社員の私が「どのような事に注意しているのか?」知りたくありませんか?
パートや就職先に「食品工場」での勤務を検討されている方には参考になる内容です。
「食品工場」と言っても作業は様々です。「電話問い合わせ」する時に役立ててください。
会社とは全く関係なく私の独断で行っておりますので、余計な「バイアス」はかかっておりません。
漠然と作業内容について記すと、とめどない状態になってしまいます。
というより「ただの日記」になってしまいます。(いやそれも面白そうですね)
今回は「作業を管理する上で注意している事を3項目」にしぼって記して参ります。
- 安全に作業する
- 滞りなく作業を進める
- 確実な製品を製造する
この3項目を記して参ります。
各種の「マニュアル本」などをそれなりに読み漁り、色々試行錯誤した結果です。
会社には評価されないので「たいした内容ではない」と勝手に判断して記します。
「食品工場」に限らず「パートさん」を多く扱っている会社では「有益なのではないかな~」と言った内容であると自負しております。
たまたまこのサイトに来てしまったとしても、「有益だったな~」「試してみよう」と思って頂きたいです。
「簡単」で「効果絶大」
だけれどもそれが「なかなか実行できない」のが真実です。
食品工場の社員にはどういう訳か「そういう人」が多いようです。(このあたりは改めて・・・)
作業を安全に進めるために
一言で「安全」と言っても幅広いです。
大きく分けると「製品の安全」とそこで働く「従業員の安全」になります。
食品を扱う上で「製品の安全」は確実なものにしなければなりません。
昨今のネット社会では何か事が起きればSMSで瞬く間に拡散してしまう世の中です。
食品・飲食業界では一般的な方でも比較的想像しやすい分野からなのか、事が起きれば「会社が無くなる程の大打撃」となってしまう事にもつながりかねません。
製品の安全
原料の取り扱いが主になります。原料の入荷から加工されて製品になり出荷されるまで確実に管理さしなければなりません。出荷したそれ以降も温度管理や取り扱いに注意しなければなりません。
温度管理が不十分ですと品質の劣化や食感の劣化、最悪な場合は腐敗・・・なんて事にもなりまねません。
このあたりは注意点を細かく上げると「キリ」がありません。
「工程管理」のチェック項目は多く、各工程のチェック表を合わせると膨大な枚数になります。
帳票管理は正直なところ辛いものがあります。大手の企業の基準に、中小の食品工場も追随しなければならないので結構な負担となります。
各工程のチェック表の記載はパートさんにもお願いしますが、肝心なところは社員が再確認と帳票のとりまとめを行う事になります。
後にチェック漏れが発覚するだけなら(大きな声で言えない)・・・ですが実際の製品に問題があってからでは取り返しがつきません。
例えばですが、家庭では多少賞味が過ぎてしまっても「調理」して食べてしまいますが、「食品工場」ではそういう訳には行きません。
会社が無くなってしまう事態にもなりかねません。
食品の「トレーサビリティ」等で非常に厳しくなっておりますので、各工程の「工程管理」必要なら帳票で証明のためチェックしなければなりません。
このように書くと「チェックする事が重要」の様になってしまいますが、確実な行程チェックを行う事で「安心して作業を進める」事ができます。
重要なのはこのチェックを「多少時間がかかっても省かない事」です。
従業員の安全
作業をする上で「整理・整頓」や「室温」の温度管理も必要です。「室温」については「原料」にあわせるため、多少「寒い」と感じるかもしれません。
加工途中の原料が乱雑になっていると「作業の邪魔」になってしまいます。
必要な時に必要な量を準備する事が、「安全」にもつながります。
「製品の安全」と「従業員の安全」は共通な点が多いです。
「従業員の安全」に注意すると必然的に「製品の安全」にもつながります。
機械の「メンテナンス」も重要です。不具合のある状態で作業を進めると、「機械の破損」そして「製品の不具合」になって現れます。
その結果パートさんにも余計な作業の負担を掛ける事になります。
作業のやり直しは精神的にもコスト的にも負担が大きいです。
機械の不具合が発生した時には「直ちに機械を止める」事が「ケガの防止」になります。
少しでも異変を感じたら「まず止める」のが基本です。
ただこれだけの事です。
しかしこの「機械を止める」と言うのがライン作業ではなかなかできないのが現実?
「機械を止めたら作業が遅れてしまう」「回りに白い目で見られる」と考えてしまうようです。
社員の仕事はこのような作業上の不安を取り除く事です。
何かしらの不具合を感じたら「直ちに作業を止める」コレが行えるよう日頃から環境を整える事が大切です。
工場によってはラインを止めると「ばかやろう!!」と怒鳴られた、と言ったような書き込みを目にした事があります。非常に残念です。
私はこのような工場はやがて衰退してしまうと考えております。
こんな工場では働きたくないですよね?
作業を滞りなく進めるために
前項では「ラインを止めると怒られた」的な内容を記しました。しかし正直なところ「そんなに急いでもそれ程変わらない」と言うのが本音です。
無理をしてラインのパートさんに負担をかけたところで「結局どこかで歪がでてしまう」ので、トータルではマイナスになってしまう事も・・・(離職したり)
「急がず慌てず」が円滑に進めるコツ
生産予定が詰まっていると「とにかく急がなくては・・・」となりがちです。
しかし、急いで行なえば「作業が速く終わる」とは限らないのが現実です。
急ぐあまり、「機械」「工程」「製品」の不具合が発生してしまう事もあります。
流れている作業が「トラブル」で止まってしまえば、急いで行った時間が「チャラ」になります。
ゆっくりでも「確実に進める」事が全行程トータルで見ると、円滑に終わらせる「コツ」かも知れません。
少なくても私の勤めている工場で効果が出ております。
私のラインは「慌てず」「落ち着いて」いるけれども予定通りに進められております。
作業を確実に進めるために
普段からパートさんと良い関係を築く事が何よりも大切です。
普段気にしている事を記します。
雑談をする
仕事中に雑談をするとは・・・会社の上司からは叱られそうですね。いや、実際あんまりひどいと嫌味を言われますよ。
「そんな事いいから機械回せ!!」とかね・・・
雑談のタイミングは「始業前」「休憩時」「ラインが少し止まった時」「段取り替え」の隙間時間などに少しずつ行います。
後は「清掃の終了時」は1日の振り返りをするのに適しています。
雑談と言ってもだいたいは「作業に関して」です。
個々の作業で気になる事を「話したくてしょうがない」のです。
その時に「面倒だな~」とか思わずに、話を引き出すように「相づちを打つ」方が後々の作業が間違えなく円滑に進みます。
どの様な内容でも「肯定的」に受け止めます。
決して「否定」したり、答えを「返答」したりしないように!!
「それなら、このように対処しますね!!」等と決めてしまわないように・・・
一見「問題解決になった」と思ってしまいがちです。
しかし「返答」をする事は「反論された」につながる事があります。
「へ~そうなんだ~」と聞くにとどめるのが「ベストな対応」です。
話をとにかく聴く
前項にも触れましたが「話を聴く」できるのなら「傾聴」の姿勢が大切です。
「多少の不満」なら「ガス抜き」になりますし、工程上の「改善活動」に大きな影響を与える事が多いからです。
パートさんからの情報が「ラインの生の声」です。
「ラインの生の声」をしっかり受け止める事により、管理者には見えないものが見えるようになります。
「雑談」からはじまった「改善」を繰り返す事により、ラインの「ブラッシュアップ」ができます。
「小さい改善」の積み重ねが円滑で安全な効率の良い運営につながります。
大きな改善はいきなり行わず「少しずつ」軌道修正するように行う方が、全体の合意を得やすいです。
どんどん聞いて、聞いて、聞きまくりましょう!!
「ていねい」な言葉で
話すときは「ていねいな言葉」を使うように意識します。雑な言葉は人を遠ざけてしまいます。
パートさんとの距離が離れれば離れる程、指示、伝達事項は伝わりにくくなります。
伝えたはずなのに「意図しない動き」をしたりします。
思った通りの指示が伝わらないのは「パートさんあるある」です!!よね?
「ていねいな言葉」でパートさんとの距離が近いほど、不具合時の連絡も円滑に伝わるようになります。結果「チョコ停」も少なくなります。
ライン運営も「安定」し、出来上がる製品の品質も「安定」します。
円滑に進んでいる時には「ありがとうございます」と各担当のパートさんに言って回りましょう。
「ありがとうございます」「いい感じです」「よろしくお願いします」「ナイスです」「いいね!」・・・
これが声掛けの「秘訣」です。
少し無理をさせてしまった時には「今日は助かりました」と付け加えましょう。
「ていねい」な動作で
「ていねいな言葉」と同じくらい大事なのが「ていねいな動作」です。
工場内はそれなりに機械の騒音があります。「言葉が伝わりにくい」状況でも、行っている動作が「いいのか」「悪いのか」は動作で伝わります。
間違えなく「円滑にすすんでいる」時には「言葉は伝わりにくくても」動作・見た目で伝わります。
多少「オーバーアクション」に身振り手振りで伝えると、指示が伝わりやすくなります。
「原料」や「器具」の取り扱いも、とにかく「ていねいに行う」事です。
「ガチャガチャ」音を立てての動作は、ラインのパートさんの心理的な不安につながります。
「何か不具合でもあったのかな~」
「私、何かしてしまったかな~」とか・・・
ラインのパートさんは「非常に敏感」です。
少しでも不安を感じると「計量している重量」が不安定になります。
場合によっては「材料の抜け」になって現れます。(検品ではじかれます)
「ラインの遅延」となって現れたりする事もあります。
脳科学的に言うと「ワーキングメモリ」が「音への注意」に使われてしまうからでしょう。
【食品工場】パートさんの管理で心がけている事 まとめ
当たり前の内容ですが、ラインが動くとつい「忘れがち」な内容です。
- 安全に作業する
- 滞りなく作業を進める
- 確実な製品を製造する
以上の3項目を軸に述べて参りました。
パートさんの取り扱い方がメインの内容になってしまいました。
人数も圧倒的に多いので工場の運営では「ポイントになる」部分です。
パートさんとの関係が良好であれば、少ない労力で最高のパフォーマンスを発揮させる事ができます。
しかし、そうでないと労力の割に上手くライン運営できません。
ライン運営の不安定は必ず「製品の品質」につながってきます。
という事で社員の仕事は「パートさんとの良い関係を築く事」になりますね。
毎日の作業をお互いに気持ちよく進めるためにも
「ありがとうございます」「いい感じです」「よろしくお願いします」・・・
このような「前向きな言葉」と「感謝」の気持ちを忘れずにライン運営して参りたいと思います。
ここまで読んでいただきありがとうございます。
皆様の会社がより良い環境となりますように・・・
コメント